Turbo mill
In order to return the reaction product occurring after flue gas cleaning back to the raw material, we have developed a mill with which the reaction product can be crushed down to the necessary grain size of between 150 and 200 microns.
The functional principle
The mill housing has welded steel construction with an infeed (Ø 120 mm and an outfeed flange at 486 x 95 mm. It is fitted with a mechanically processed, hinged door section with ring seal and flanged material feed connection.
A solenoid switch and a motor standstill monitoring device secure the door against unintentional opening.
The turbo mill is fitted with an inclined feed and a hinged permanent magnet for separation of metal components.
The drive motor is flanged onto the mill housing and takes up the rotor directly. The motor bearing is kept free of dust by blowing of low-volume compressed air in between the motor flange plate and the mill housing.
The milling unit itself consists of a solid, machined rotor (Ø 300 mm) made of special steel. The stator, which also consists of special steel, is a pulveriser grid with an insert in milled steel. The milled goods are fed continually to the mill using a metering screw.
The rotating milling tool (approx. 4000-5000 rpm) disintegrates the milled goods and presses it through the milling grille, after which it falls into the hopper mounted underneath the mill.
The milled material is fed out via a chamber lock (two opposing locked flaps) or a cellular wheel sluice.
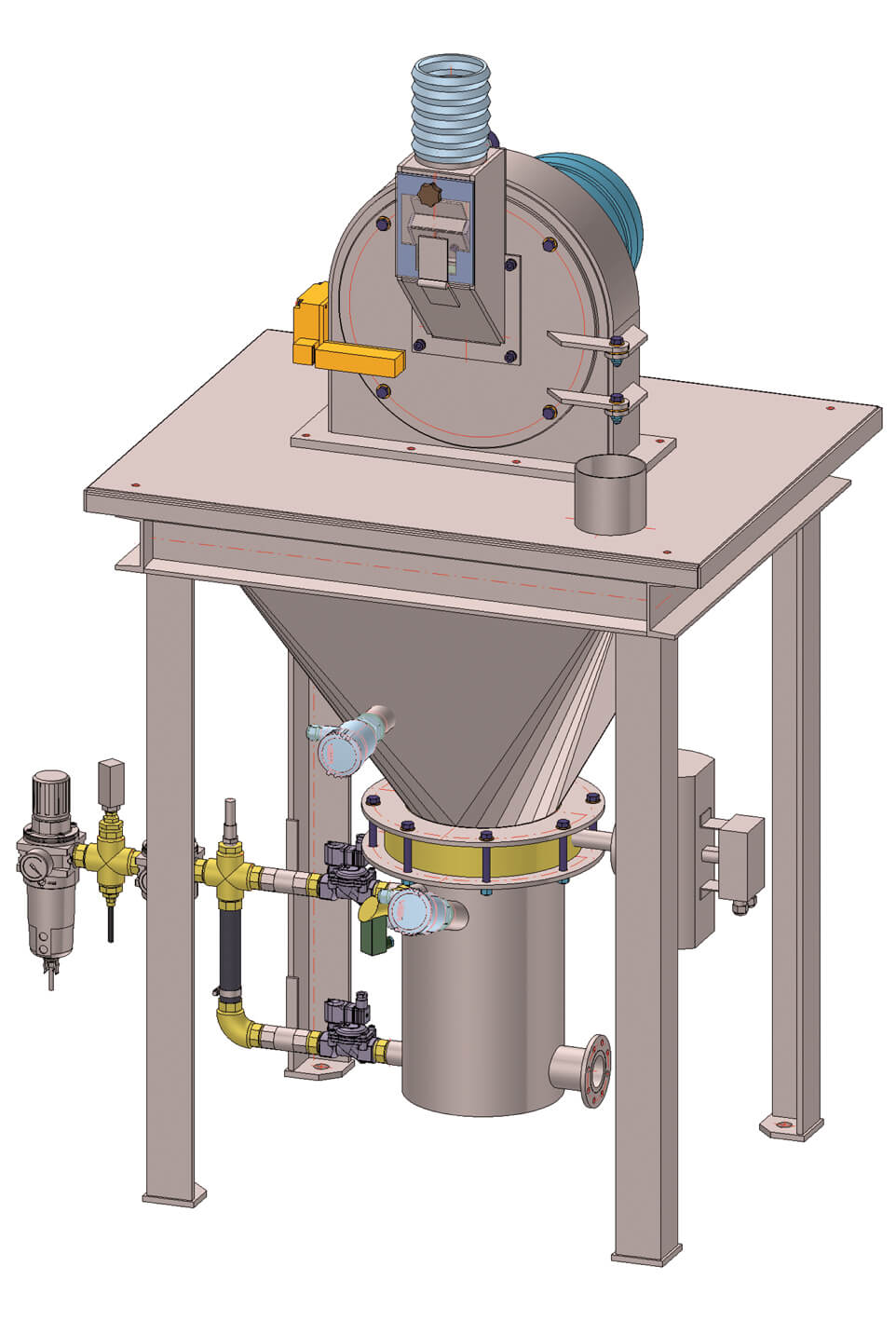
Advantages
- Heavy-duty construction
- Specially adapted to grinding stock
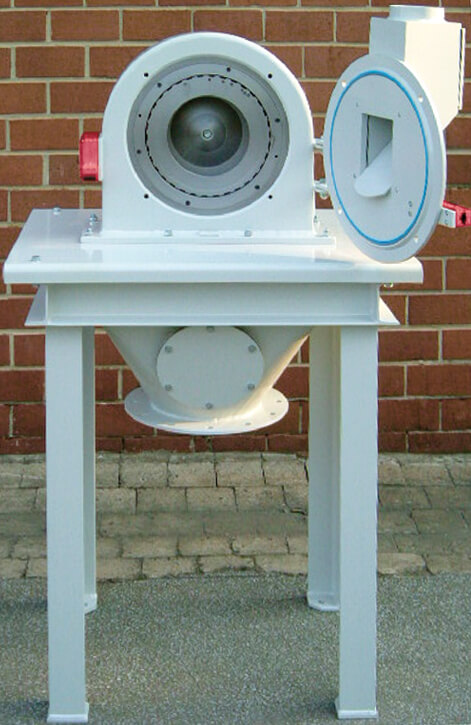